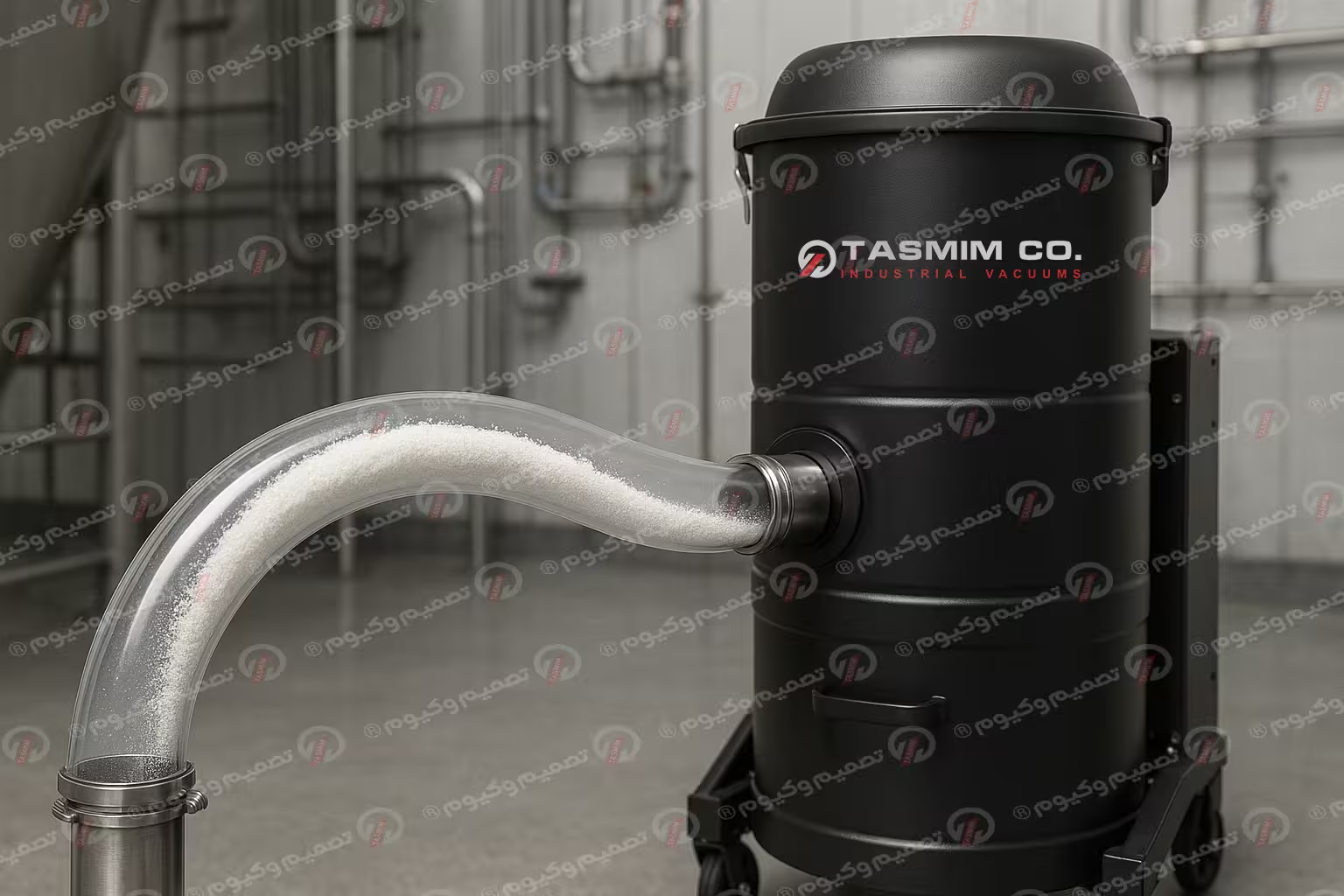
سیستم انتقال مواد چیست و چگونه بهرهوری تولید را چند برابر میکند؟
در دنیای رقابتی و پرتلاطم صنعت امروز، برندهایی مانند تصمیم وکیوم با ارائه راهکارهایی هوشمندانه برای انتقال مواد، به تولیدکنندگان کمک میکنند تا بهرهوری را افزایش داده و هزینهها را بهطور چشمگیری کاهش دهند.
یکی از عوامل کلیدی اما کمتر مورد توجه قرار گرفته، شیوه انتقال مواد در خطوط تولید است؛ فرآیندی که اگرچه پشتصحنه به نظر میرسد، اما نقش حیاتی در سرعت، کیفیت و هزینه تمامشده محصول ایفا میکند. در بسیاری از صنایع، از غذا و دارو گرفته تا صنایع شیمیایی و معدنی، انتقال مواد یکی از چالشهای اساسی بهشمار میرود.
استفاده از روشهای سنتی مانند نوار نقالههای ساده یا انتقال مواد بهصورت دستی، اغلب با اتلاف مواد، آلودگی، کاهش کیفیت و هزینههای بالای عملیاتی همراه است. اما پیشرفت فناوری راه را برای تحول در این بخش هموار کرده است. سیستمهای مدرن انتقال مواد مانند سیستم انتقال پنوماتیک و سیستم انتقال با خلاء، با اتکا به فناوریهای نوین، میتوانند تا بیش از ۳۰ درصد در کاهش هزینههای تولید مؤثر باشند، بدون آنکه کیفیت یا ایمنی فرآیند تولید به خطر بیفتد.
سیستم انتقال پودری چیست و چه کاربردی دارد؟
سیستم انتقال پودری (Powder Conveying System) به مجموعهای از تجهیزات و روشها گفته میشود که برای جابجایی مواد پودری از یک نقطه به نقطه دیگر در فرآیند تولید یا بستهبندی مورد استفاده قرار میگیرند. این سیستمها با توجه به نوع ماده، فاصله انتقال، ظرفیت مورد نیاز و شرایط محیطی، میتوانند در اشکال مختلفی طراحی و اجرا شوند.
خطر، انتخابی کارآمد و ایمن برای این بخشهاست. همچنین کاهش نیاز به تجهیزات مکانیکی باعث افزایش ایمنی و کاهش هزینههای نگهداری در شرایط سخت پتروشیمی میشود.
اهداف اصلی استفاده از سیستم انتقال مواد پودری
- انتقال سریع، ایمن و بهداشتی مواد پودری
- کاهش اتلاف مواد و جلوگیری از آلودگی محیط
- افزایش بهرهوری و کاهش وابستگی به نیروی انسانی
- حفظ یکنواختی و کیفیت مواد در حین جابجایی
انواع سیستم انتقال مواد پودری
- سیستم انتقال پنوماتیک (Pneumatic Conveying)
- سیستم انتقال با خلاء ( Vacuum Conveying)
- سیستم اسکرو یا مارپیچی (Screw Conveyor)
- سیستم دیسکی یا کششی (Disc or Tubular Drag Conveyor)
- نقاله ارتعاشی یا ویبراتوری
سیستم انتقال پنوماتیک چیست و چگونه کار می کند؟
سیستم انتقال پنوماتیک مواد خشک و پودری را از طریق خطوط لولهی بسته و با استفاده از جریان هوا یا گاز تحت فشار منتقل میکند. این انتقال به کمک تجهیزاتی مانند فن، بلوئر روتس یا کمپرسور انجام میشود و راهحلی مقرونبهصرفه و انعطافپذیر برای انتقال مواد گرانولی و پودری به شمار میآید.
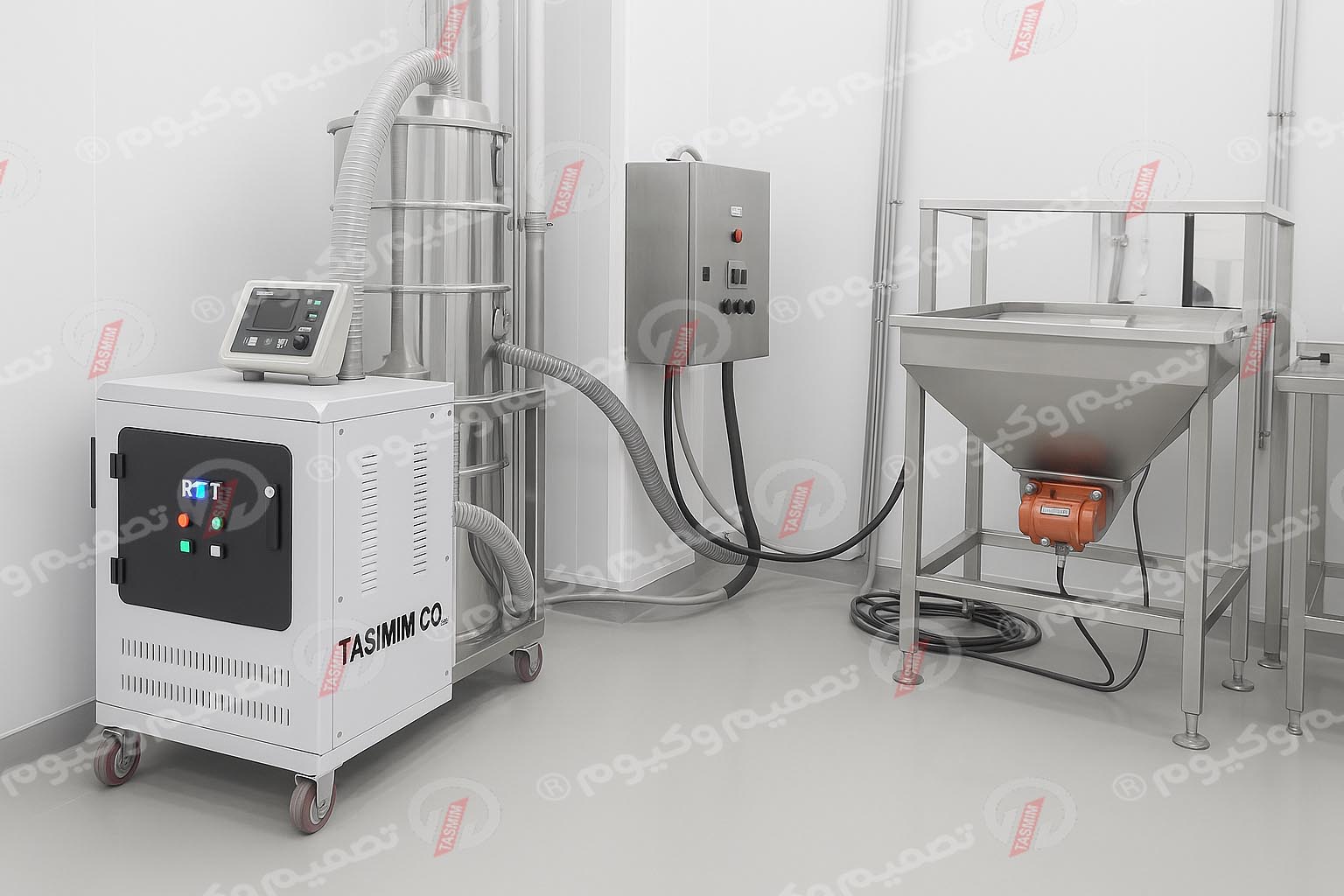
کاربرد سیستم انتقال پنوماتیک در صنایع
- صنایع غذایی و نوشیدنی
در این صنایع، رعایت بهداشت و جلوگیری از آلودگی مواد بسیار حیاتی است. سیستمهای انتقال پنوماتیک با انتقال بدون تماس مستقیم و کاملاً بسته، از ورود ذرات خارجی، گردوغبار یا آلودگی میکروبی به مواد غذایی جلوگیری میکنند. همچنین بهدلیل انتقال نرم و بدون ضربه، کیفیت مواد حفظ میشود. این سیستمها برای انتقال آرد، شکر، قهوه، ادویهجات، پودر کاکائو، غلات و… بسیار مناسباند.
- داروسازی
صنعت داروسازی به دقت بالا، ایمنی، و شرایط کاملاً استریل نیاز دارد. سیستم پنوماتیک امکان انتقال پودرها، گرانولها و مواد حساس دارویی را بدون تماس با محیط یا اپراتور فراهم میکند. طراحی بهداشتی، قابلیت شستوشو (CIP)، و حداقل تماس مکانیکی از مزایای حیاتی این سیستمها در این صنعت است.
- صنایع شیمیایی و شویندهها
در این صنایع، مواد معمولاً خورنده، خطرناک یا قابل اشتعال هستند. سیستمهای پنوماتیک بهدلیل ساختار بسته و بدون نشت، مانع از تماس مستقیم اپراتورها با این مواد میشوند. همچنین، این سیستمها ریسک آتشسوزی، انفجار یا نشت را نسبت به سیستمهای مکانیکی کاهش میدهند و ایمنی محیط کار را بهطور چشمگیری بالا میبرند.
- صنایع نوین و تخصصی
در صنایعی مانند تولید باتری، نانومواد، مواد کامپوزیتی و فناوریهای نوین، دقت، تمیزی محیط و کنترل فرآیند از اهمیت بالایی برخوردار است. سیستم انتقال پنوماتیک با قابلیت سفارشیسازی بالا، عدم آلودگی، و عملکرد دقیق، راهحلی ایدهآل برای این نوع صنایع محسوب میشود.
- پتروشیمی
در مجتمعهای پتروشیمی، حجم زیادی از مواد پودری یا گرانولی مانند کاتالیستها، پلیمرها، یا مواد افزودنی نیاز به جابجایی دارند. سیستم پنوماتیک با امکان انتقال در مسافتهای زیاد، مسیرهای پیچیده و محیطهای پرخطر، انتخابی کارآمد و ایمن برای این بخشهاست. همچنین کاهش نیاز به تجهیزات مکانیکی باعث افزایش ایمنی و کاهش هزینههای نگهداری در شرایط سخت پتروشیمی میشود.
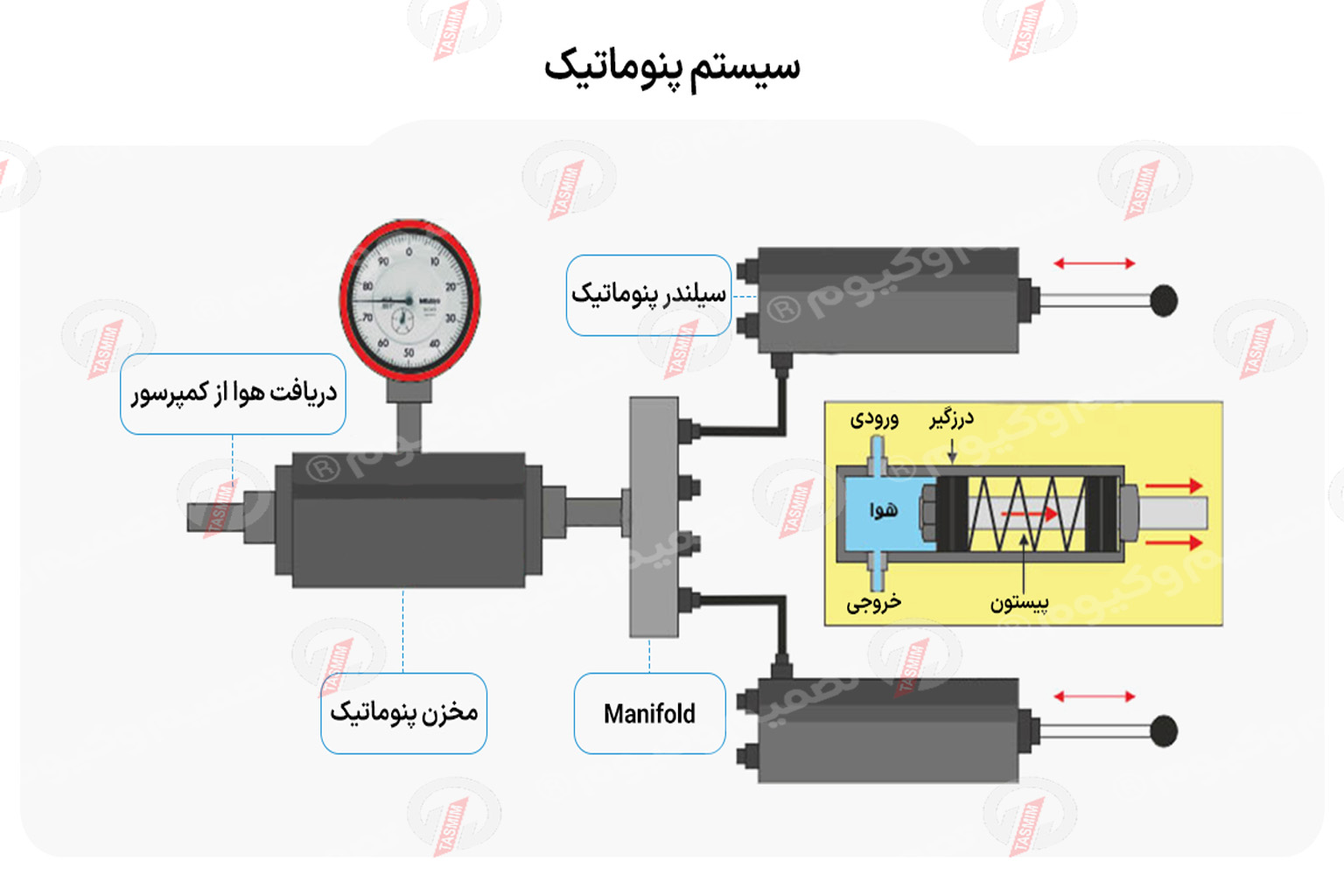
انواع سیستم انتقال پنوماتیک
سیستمهای پنوماتیک به دو نوع اصلی تقسیم میشوند:
1- فاز رقیق (Lean Phase):
1-1 فاز رقیق رقیق (Dilute Phase):
- سرعت انتقال بیش از ۱۷–۱۸ متر بر ثانیه
- فشار یا خلأ پایین (کمتر از ۰.۱ بار)
- ذرات بهصورت معلق در جریان گاز حرکت میکنند
- نسبت جرم مواد به هوا (Solids Loading Ratio) پایین
- مناسب برای مواد سبک و غیر ساینده
- تجهیزات مورد استفاده: فن یا بلوئر
1-2 فاز میانی (Medium Phase):
- سرعت انتقال مشابه حالت قبل
- فشار تا ۰.۳۵ بار
- ذرات همچنان در جریان هوا
- تجهیزات رایج: بلوئر روتس
2- فاز غلیظ (Dense Phase):
- سرعت گاز بین ۶ تا ۱۸ متر بر ثانیه
- فشار بالای ۱ بار
- در سرعتهای پایین، حرکت تودهای یا موجی ذرات
- مناسب برای مواد شکننده یا ساینده
- تجهیزات: کمپرسور یا پمپ رینگ مایع
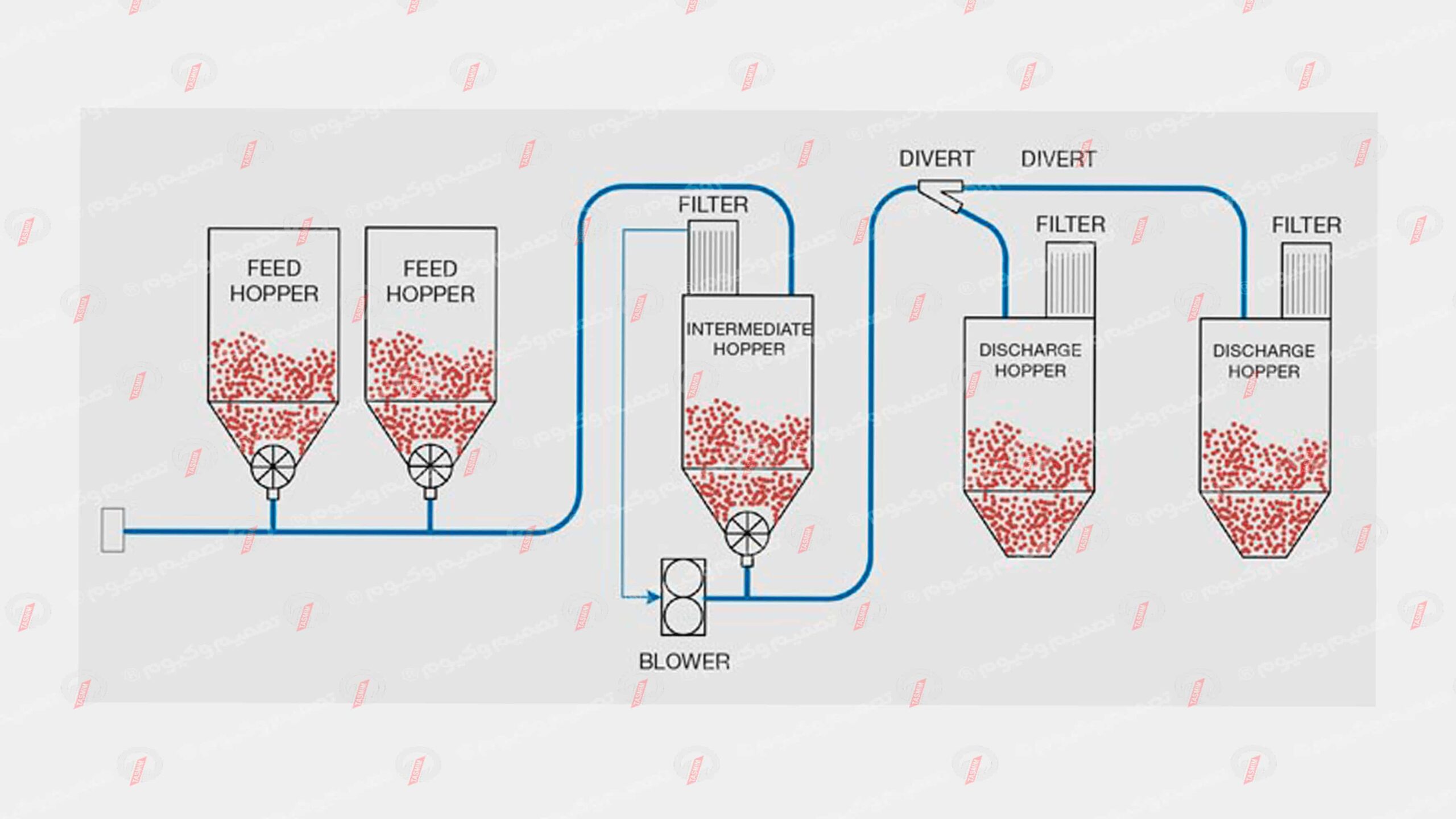
اجزای اصلی سیستم انتقال پنوماتیک
- نقطه ورود مواد
- خطوط انتقال (لولهها)
- نقطه تخلیه مواد
- تجهیزات ایجاد فشار یا مکش (مانند کمپرسور یا بلوئر)
مزایای سیستم انتقال پنوماتیک
- قابلیت نصب در مسیرهای افقی، عمودی یا پیچیده
- سیستم کاملاً بسته و بدون نشت گرد و غبار
- نگهداری آسان با قطعات متحرک کمتر
- مناسب برای فضاهای محدود
- امکان تخلیه از چند نقطه
- محافظت از مواد در برابر آلودگی یا تخریب
معایب سیستم انتقال پنوماتیک
- بازده کمتر نسبت به سیستمهای مکانیکی در انتقال حجم بالا
- نیاز به سیستم غبارگیر بزرگ در انتهای مسیر
- عملکرد محدود برای مواد چسبنده، مرطوب یا با چگالی بالا
نکات مهم در طراحی سیستم انتقال پنوماتیک
- اندازه و شکل ذرات
- درصد رطوبت مواد و هوا
- چگالی ظاهری و توانایی سیال شدن
- زوایای جریان، لغزش و انباشت
- ظرفیت و مسافت انتقال
- دمای محیط و مواد
نمونه اجرای واقعی
در یکی از پروژههای شرکت تصمیموکیوم در کارخانهای فعال در صنعت پلیمر، پیادهسازی سیستم انتقال پنوماتیک باعث کاهش ۴۰٪ در هزینههای نگهداری سالانه و افزایش ۲۵٪ در سرعت انتقال مواد شد. بازگشت سرمایه در کمتر از ۹ ماه محقق شد.سیستم انتقال پنوماتیک روشی مؤثر، تمیز و اقتصادی برای جابجایی مواد پودری و گرانولی است. این سیستم با قابلیت انتقال در مسیرهای پیچیده، جلوگیری از آلودگی، اشغال فضای کم و نگهداری ساده، انتخابی ایدهآل برای بسیاری از صنایع است. با وجود محدودیتهایی در انتقال مواد خاص، در اغلب کاربردها، کارآمد و قابلاعتماد است.
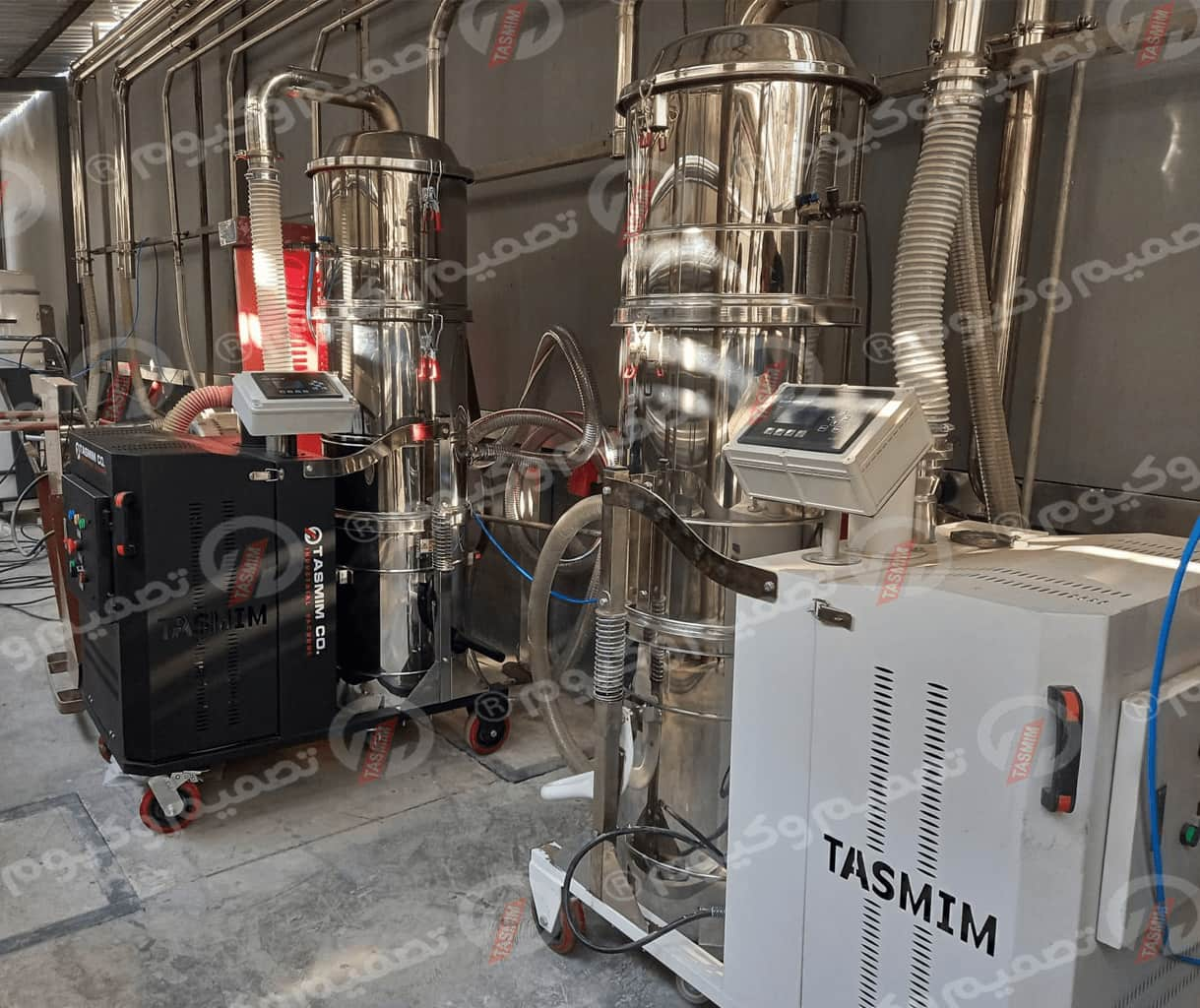
سیستم انتقال با خلاء چیست و چه کاربردی دارد؟
سیستم انتقال مواد با خلاء یکی از مدرنترین و پاکترین روشهای انتقال پودرها و مواد گرانولی سبک در صنایع حساس است. در این روش، مواد به کمک مکش ایجادشده توسط پمپ وکیوم از مخزن یا قیف تغذیه، وارد خطوط انتقال شده و بدون دخالت هوا یا رطوبت اضافی، به مقصد منتقل میشوند. این سیستم به دلیل بسته بودن کامل مسیر انتقال، ایمنی، بهداشت و کیفیت انتقال را در سطح بسیار بالایی تضمین میکند.
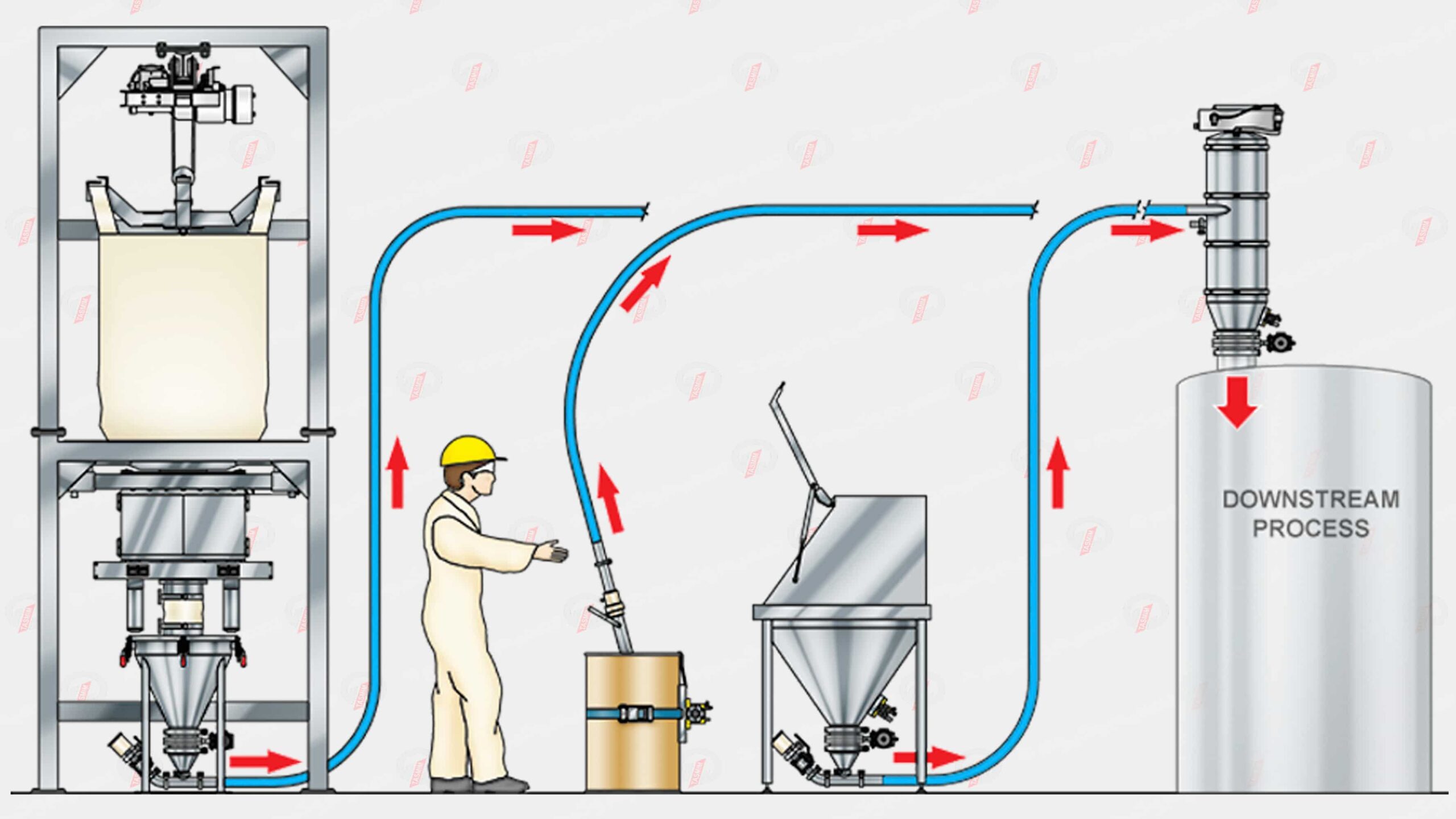
کاربرد سیستم انتقال با خلاء در صنایع
- صنایع غذایی و نوشیدنی
در این صنایع، رعایت بهداشت و جلوگیری از آلودگی مواد بسیار حیاتی است. سیستمهای انتقال پنوماتیک با انتقال بدون تماس مستقیم و کاملاً بسته، از ورود ذرات خارجی، گردوغبار یا آلودگی میکروبی به مواد غذایی جلوگیری میکنند. همچنین بهدلیل انتقال نرم و بدون ضربه، کیفیت مواد حفظ میشود. این سیستمها برای انتقال آرد، شکر، قهوه، ادویهجات، پودر کاکائو، غلات و… بسیار مناسباند.
- داروسازی
صنعت داروسازی به دقت بالا، ایمنی، و شرایط کاملاً استریل نیاز دارد. سیستم پنوماتیک امکان انتقال پودرها، گرانولها و مواد حساس دارویی را بدون تماس با محیط یا اپراتور فراهم میکند. طراحی بهداشتی، قابلیت شستوشو (CIP)، و حداقل تماس مکانیکی از مزایای حیاتی این سیستمها در این صنعت است.
- صنایع شیمیایی و شویندهها
در این صنایع، مواد معمولاً خورنده، خطرناک یا قابل اشتعال هستند. سیستمهای پنوماتیک بهدلیل ساختار بسته و بدون نشت، مانع از تماس مستقیم اپراتورها با این مواد میشوند. همچنین، این سیستمها ریسک آتشسوزی، انفجار یا نشت را نسبت به سیستمهای مکانیکی کاهش میدهند و ایمنی محیط کار را بهطور چشمگیری بالا میبرند.
- صنایع نوین و تخصصی
در صنایعی مانند تولید باتری، نانومواد، مواد کامپوزیتی و فناوریهای نوین، دقت، تمیزی محیط و کنترل فرآیند از اهمیت بالایی برخوردار است. سیستم انتقال پنوماتیک با قابلیت سفارشیسازی بالا، عدم آلودگی، و عملکرد دقیق، راهحلی ایدهآل برای این نوع صنایع محسوب میشود.
در مجتمعهای پتروشیمی، حجم زیادی از مواد پودری یا گرانولی مانند کاتالیستها، پلیمرها، یا مواد افزودنی نیاز به جابجایی دارند. سیستم پنوماتیک با امکان انتقال در مسافتهای زیاد، مسیرهای پیچیده و محیطهای پرخطر، انتخابی کارآمد و ایمن برای این بخشهاست. همچنین کاهش نیاز به تجهیزات مکانیکی باعث افزایش ایمنی و کاهش هزینههای نگهداری در شرایط سخت پتروشیمی میشود
انواع سیستم انتقال با خلاء:
1. سیستم انتقال با خلاء در فاز رقیق (Dilute Phase Vacuum Conveying)
در این سیستم، ذرات بهصورت معلق در جریان هوا (یا گاز) با سرعت بالا و فشار منفی پایین منتقل میشوند.
ویژگیهای سیستم انتقال با خلاء در فاز رقیق
- سرعت انتقال: بالاتر از 15-20 متر بر ثانیه
- فشار خلاء: کم (حدود -0.2 تا -0.5 بار)
- انتقال پیوسته و سریع
- نسبت پایین جرم مواد به هوا (Solids Loading Ratio)
- مناسب برای مواد سبک، غیر ساینده و با دانهبندی ریز
کاربردهای سیستم انتقال با خلاء در فاز رقیق
- انتقال آرد، شکر، پودر قهوه، مواد دارویی و شیمیایی سبک
در این سیستم، ذرات بهصورت معلق در جریان هوا (یا گاز) با سرعت بالا و فشار منفی پایین منتقل میشوند.
2. سیستم انتقال با خلاء در فاز غلیظ (Dense Phase Vacuum Conveying)
ویژگیهای سیستم انتقال با خلاء در فاز غلیظ
- سرعت انتقال: 5 تا 12 متر بر ثانیه
- فشار خلاء: بالا (تا -0.8 بار یا بیشتر)
- نسبت بالای جرم مواد به هوا (Solids Loading Ratio)
- انتقال موجی یا ضربهای مواد (Slug یا Plug)
- مناسب برای مواد شکننده، ساینده یا با چگالی بالا
کاربردهای سیستم انتقال با خلاء در فاز غلیظ
- انتقال رزینها، دانههای پلاستیک، پودر فلزات، مواد حساس و گرانقیمت
اجزای اصلی سیستم انتقال با خلاء
- پمپ خلاء (Vacuum Pump)
- ورودی مواد (Feeding Point)
- لولههای انتقال (Transfer Lines)
- جداکننده و فیلتر(Separator & Filter)
- مخزن تخلیه (Discharge Hopper)
- فیلتر نهایی (HEPA / Dust Filter)
- سیستم کنترل
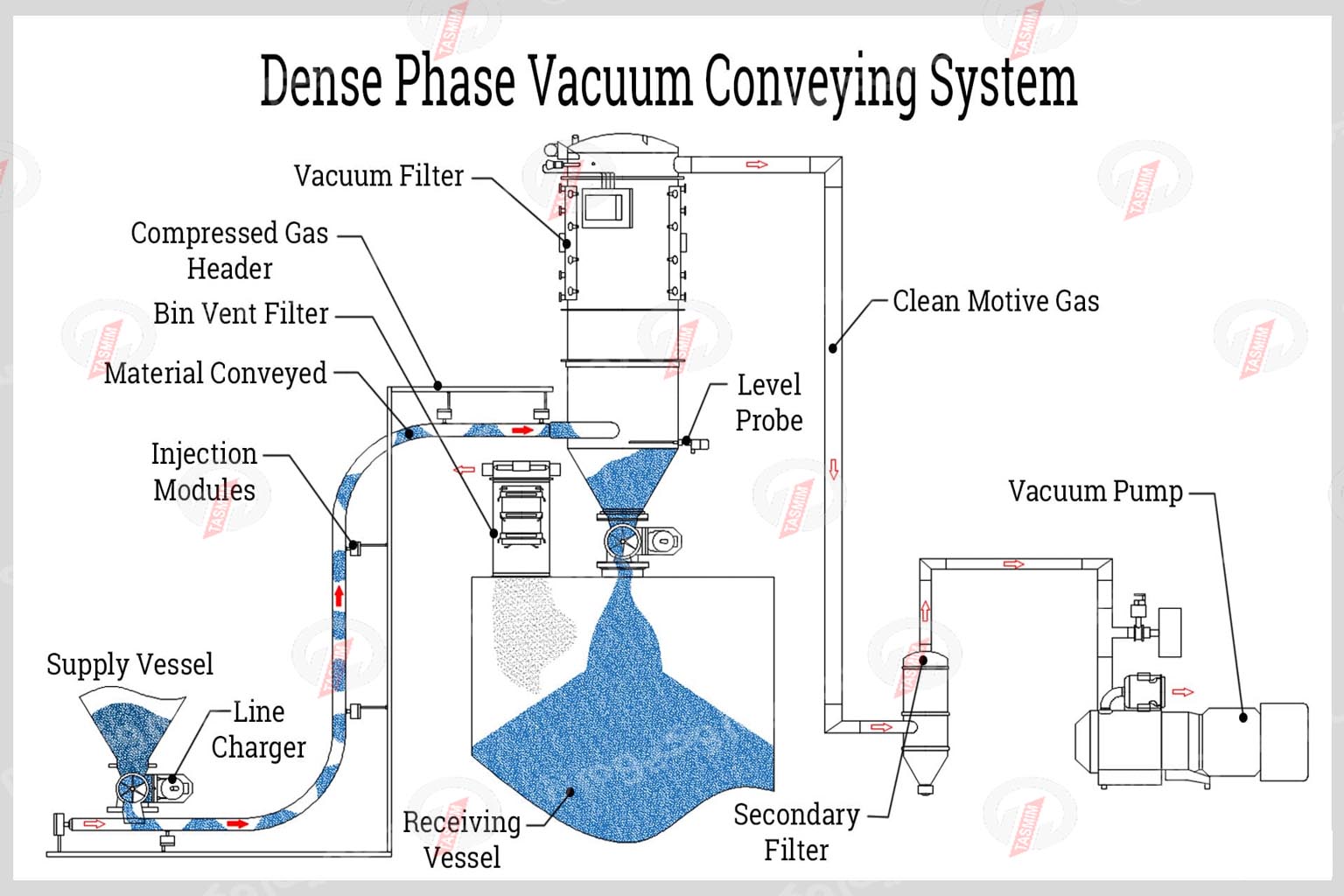
مزایای سیستم انتقال با خلاء
- سیستم کاملاً بسته و ایمن
- عدم تماس مکانیکی با مواد
- مناسب برای فضاهای محدود
- راهاندازی و نگهداری آسان
- امکان انتقال از چند نقطه به یک مقصد یا بالعکس
- عملکرد بیصدا و کم لرزش
معایب سیستم انتقال با خلاء
- ظرفیت محدود نسبت به سیستمهای تحت فشار
- طول مسیر محدود
- افت راندمان در مواد بسیار سنگین یا مرطوب
- نیاز به فیلترهای دقیق و تعویض منظم
- مصرف انرژی بالا در فشارهای خلأ بالا
- حساسیت به نشتی هوا
نکات مهم در طراحی سیستم خلاء
- انتخاب پمپ خلا مناسب بر اساس حجم و نوع ماده
- مسیر کوتاه و بدون پیچوخم زیاد برای کاهش افت فشار
- سرعت انتقال کنترلشده تا از آسیب یا گرفتگی جلوگیری شود
- استفاده از سپراتور و فیلتر برای جداسازی مواد از هوا و محافظت پمپ
- جلوگیری از نشت هوا با اتصالات محکم و کنترل فشار
- انتخاب متریال مناسب طبق نوع ماده انتقالی
- امکان دسترسی آسان برای نگهداری و تعمیرات
- سیستم کنترل و مانیتورینگ برای بهینهسازی عملکرد
نمونه اجرای واقعی
در یکی از پروژههای اخیر شرکت تصمیموکیوم برای یک کارخانه داروسازی، پیادهسازی سیستم Vacuum Conveying موجب کاهش ۶۰٪ گردوغبار محیطی و افزایش ۳۰٪ در دقت و سرعت انتقال مواد شد. این پروژه تنها طی ۶ ماه به بازگشت سرمایه رسید و اکنون به یکی از خطوط اصلی تولید آن مجموعه تبدیل شده است.
سیستم انتقال با خلا روشی کارآمد، بهداشتی و ایمن برای جابجایی مواد پودری و گرانولی است. این سیستم با انتقال ملایم مواد، جلوگیری از آلودگی و قابلیت نصب در فضاهای محدود، گزینهای مناسب و مطمئن برای صنایع حساس به شمار میآید.
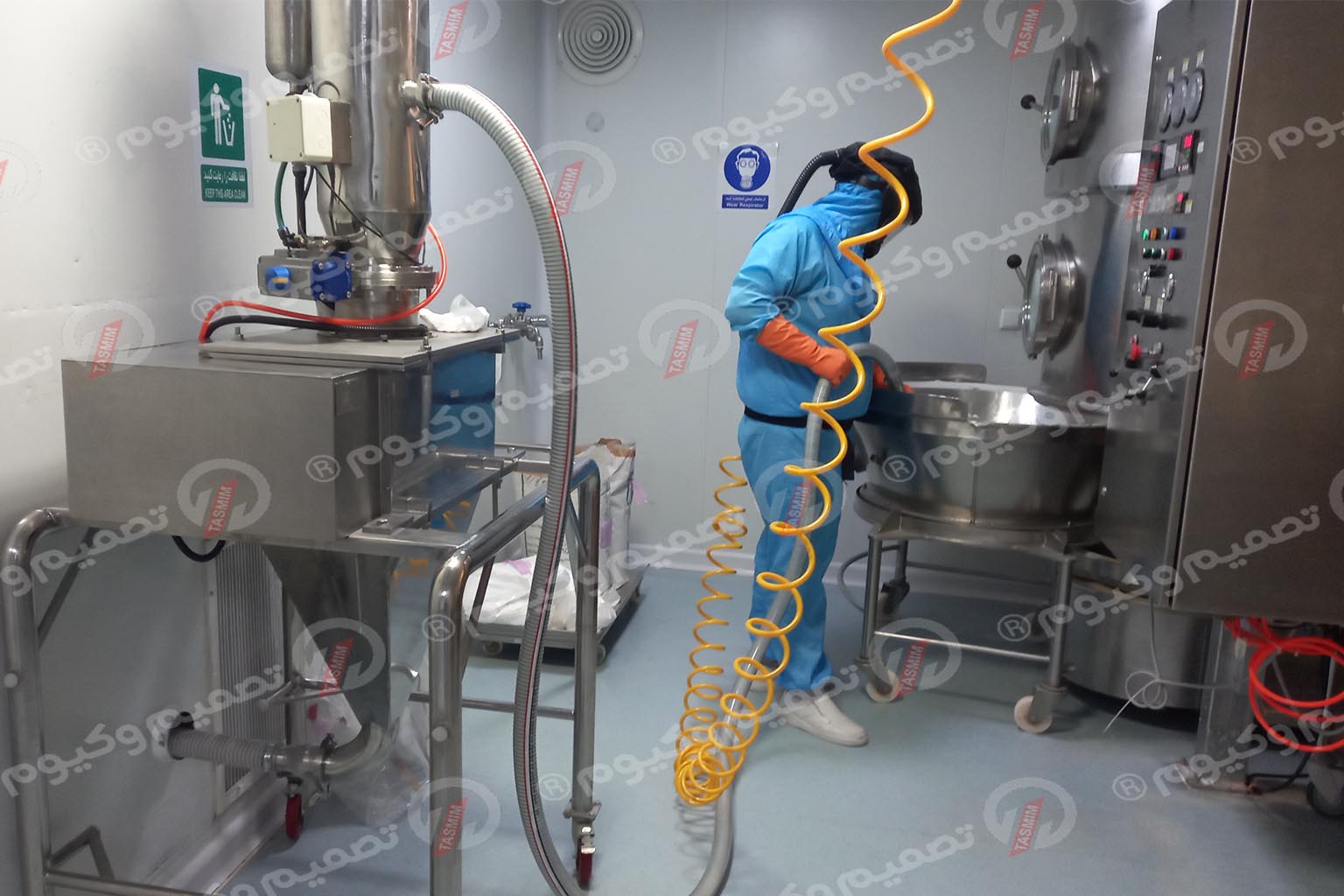
سیستم انتقال اسکرو یا مارپیچی چیست و چه کاربردی دارد؟
سیستم انتقال اسکرو(Screw Conveyor System)، که با نامهای نقاله مارپیچی یا اسکرو کانوایر نیز شناخته میشود، یکی از رایجترین و سادهترین روشهای انتقال مواد جامد پودری یا دانهای است. در این سیستم، مواد توسط یک مارپیچ دوار که داخل یک لوله یا شیار فلزی قرار دارد، از یک نقطه به نقطه دیگر منتقل میشوند.
انواع سیستم انتقال اسکرو یا مارپیچی
- اسکرو افقی (Horizontal Screw Conveyor):
رایجترین نوع؛ برای انتقال مواد در مسیر افقی یا با شیب کم.
- اسکرو شیبدار (Inclined Screw Conveyor):
برای انتقال مواد در مسیرهای با زاویه؛ راندمان آن با افزایش زاویه کاهش مییابد.
- اسکرو عمودی (Vertical Screw Conveyor):
برای انتقال مواد به سمت بالا در فضاهای محدود؛ نیاز به طراحی دقیق دارد.
- اسکرو لولهای (Tubular Screw):
مارپیچ داخل لوله بسته میچرخد؛ مناسب برای مواد سمی، گرد و غباری یا حساس.
- اسکرو U شکل (U-trough Screw):
مارپیچ در داخل ناودان U شکل قرار دارد؛ اغلب در صنایع غذایی و ساختمانی.
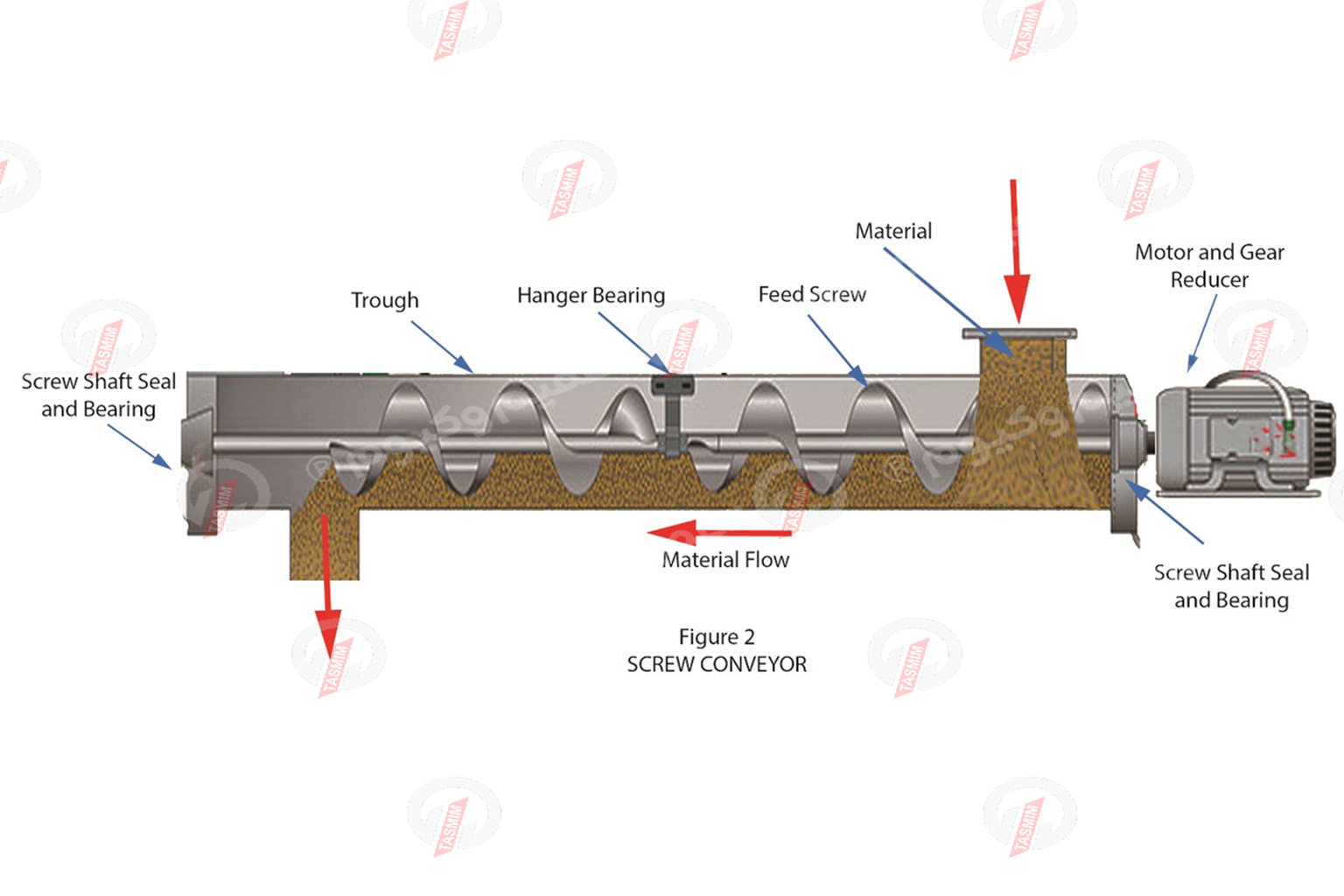
اجزای اصلی سیستم اسکرو یا مارپیچی
- مارپیچ (Helix یا Screw Blade)
قطعهای چرخان با شکل حلزونی است که وظیفه دارد مواد را به جلو هدایت کند. این تیغهها میتوانند به صورت پیوسته یا قطعهقطعه باشند.
- شفت (Shaft)
محور مرکزی که مارپیچ روی آن سوار است و همراه آن میچرخد. شفت به موتور متصل میشود و نیروی چرخشی را به مارپیچ منتقل میکند.
- محفظه یا بدنه (Trough or Tube)
ساختاری فلزی که مارپیچ درون آن حرکت میکند. این محفظه میتواند باز (U شکل) یا بسته (لولهای) باشد، بسته به نوع کاربرد و میزان گرد و غبار یا آلودگی ماده.
- موتور و گیربکس
مجموعهای که نیروی لازم برای چرخش مارپیچ را تأمین میکند. گیربکس سرعت موتور را کاهش داده و گشتاور لازم برای انتقال ماده را فراهم میسازد.
- یاتاقانها (Bearings):
برای نگهداشتن و پشتیبانی از شفت و مارپیچ استفاده میشوند و به کاهش اصطکاک و افزایش طول عمر قطعات کمک میکنند.
- دریچههای ورود و خروج:
نقاطی برای ورود مواد اولیه به سیستم و تخلیه آنها در مقصد. این دریچهها معمولاً بهگونهای طراحی میشوند که جریان مواد قابل کنترل باشد.
مزایای سیستم اسکرو یا مارپیچی
- ساختار ساده
- هزینه کمتر
معایب سیستم اسکرو یا مارپیچی
- محدودیت در انتقال مواد در مسیرهای طولانی
- مستعد سایش بهخصوص در مواد خورنده یا ساینده
- افزایش مصرف انرژی در انتقالهای شیبدار یا عمودی
- امکان آسیب به مواد حساس یا شکننده
- ایجاد گرما در سرعتهای بالا (در برخی کاربردها)
- هزینه تعمیر و نگهداری بالا
صنایع مناسب برای سیستم اسکرو یا مارپیچی
- صنایع غذایی
- صنایع دارویی
- صنایع شیمیایی
- صنایع معدنی و سیمان
- صنایع پلاستیک و پتروشیمی
- صنایع کشاورزی
- صنایع کاغذ و بازیافت
- صنایع فلزی و ریخته گری
سیستم نقاله ارتعاشی چیست و چه کاربردی دارد؟
سیستم نقاله ارتعاشی، یک نوع سیستم انتقال است که برای حرکت دادن مواد روی سطح افقی یا شیبدار از حرکات ارتعاشی استفاده میکند. این ارتعاشات معمولاً توسط الکتروموتور یا مکانیزمهای ارتعاشی ایجاد میشود و بهطور معمول برای جابجایی مواد پودری، گرانولی، یا حتی مواد بزرگتر و سنگینتر در صنایع مختلف استفاده میشود.
انواع نقاله ارتعاشی
- نقاله ارتعاشی خطی (Linear Vibratory Conveyor):
این سیستم حرکت مستقیم (خطی) به مواد منتقل میکند. معمولاً در مواردی استفاده میشود که نیاز به انتقال مواد با دقت بالا و بهطور یکنواخت وجود دارد.
- نقاله ارتعاشی دایرهای (Circular Vibratory Conveyor):
در این سیستم، حرکت مواد بهطور دایرهای یا چرخشی انجام میشود. این نوع سیستمها معمولاً برای انتقال مواد با حجم بیشتر یا برای تخلیه مواد بهطور یکنواخت از مخازن استفاده میشوند.
- نقاله ارتعاشی با زاویه (Inclined Vibratory Conveyor):
این سیستم برای جابجایی مواد به سمت بالا یا در زاویه خاصی طراحی میشود. معمولاً برای انتقال مواد به ارتفاعهای بالاتر یا انتقال در فضاهای محدود کاربرد دارد.
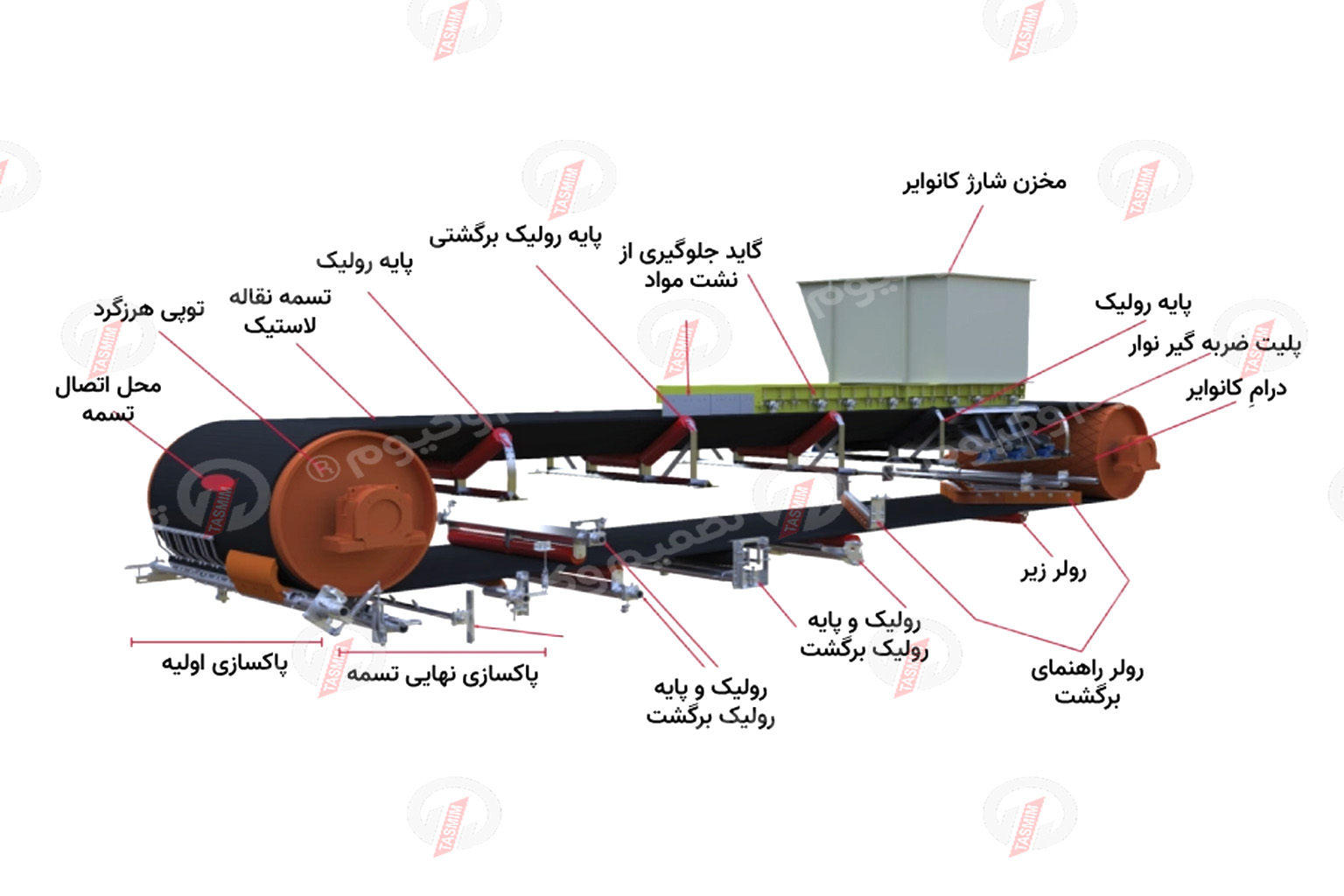
اجزای اصلی سیستم نقاله ارتعاشی
- بستر یا سطح نقاله (Conveyor Bed):
سطحی است که مواد روی آن حرکت میکنند. این بستر معمولاً از فولاد ضدزنگ یا مواد مقاوم در برابر سایش ساخته میشود.
- الکتروموتور و محرک ارتعاشی:
موتور اصلی است که نیروی لازم برای ایجاد ارتعاشات را فراهم میکند. این موتور میتواند بهطور مستقیم یا از طریق مکانیزمهای خاصی (مثل چرخ دندهها یا چرخهای وزنی) به حرکت درآید.
- مکانیزم ارتعاشی:
اجزای مکانیکی هستند که ارتعاشات تولید میکنند و به نقاله منتقل میکنند. این سیستم میتواند شامل فنرها، وزنهها و سایر تجهیزات باشد.
- فنرها (Springs):
برای ایجاد ارتعاش و انتقال حرکت به سطح نقاله، از فنرهای خاص استفاده میشود. این فنرها میتوانند در تنظیم شدت و فرکانس ارتعاشات نقش داشته باشند.
- سیستم کنترل:
برای تنظیم و کنترل شدت ارتعاشات، از سیستمهای الکترونیکی و پنوماتیک استفاده میشود. این سیستمها اجازه میدهند که حرکت نقاله بهطور دقیق و کنترلشده باشد.
مزایای سیستم نقاله ارتعاشی
- انتقال مواد حساس و شکننده:
این سیستم به دلیل استفاده از ارتعاشات ملایم، برای انتقال مواد شکننده و حساس به فشار مناسب است.
- کاربرد در مسیرهای پیچیده:
این سیستمها میتوانند در مسیرهای پیچیده یا با شیبهای مختلف به راحتی مواد را انتقال دهند.
- نصب و نگهداری ساده:
سیستمهای نقاله ارتعاشی معمولاً نیاز به تعمیرات و نگهداری کمتری دارند و بهطور نسبی نصب سادهای دارند.
- عدم نیاز به روغنکاری مداوم:
بسیاری از مدلهای نقاله ارتعاشی نیاز به روغنکاری مداوم ندارند، که این امر باعث کاهش هزینههای نگهداری میشود.
- کاهش خطر آلودگی:
در سیستمهای ارتعاشی، بهویژه در صنایع غذایی و دارویی، مواد بهصورت بسته انتقال مییابند و این امر میتواند آلودگی را کاهش دهد.

معایب سیستم نقاله ارتعاشی
- محدودیت در ظرفیت انتقال
نقالههای ارتعاشی برای جابجایی مواد در ظرفیتهای بالا مناسب نیستند و ممکن است در حجمهای بزرگ به کارآیی پایینتری برسند.
- هزینه اولیه بالا:
طراحی و ساخت سیستمهای نقاله ارتعاشی به دلیل نیاز به موتور و مکانیزمهای دقیقتر، هزینه اولیه بالاتری نسبت به برخی سیستمهای انتقال دیگر دارند.
- نیاز به تنظیم دقیق:
برای دستیابی به عملکرد بهینه، این سیستمها نیاز به تنظیمات دقیق و مانیتورینگ دارند، بهویژه در صورت تغییر نوع یا اندازه مواد.
- صدای بلند:
در برخی از مدلها، سیستم ارتعاشی ممکن است نویز زیادی تولید کند که در محیطهای خاص مانند محیطهای پزشکی یا داروسازی میتواند مشکلساز باشد.
- آسیب به مواد حساس:
در صورتی که تنظیمات ارتعاشات به درستی انجام نشود، ممکن است آسیبهای جزئی به مواد حساس مانند مواد پودری یا شکننده وارد شود.
صنایع مناسب برای سیستم نقاله ارتعاشی
- صنایع غذایی
- صنایع دارویی
- صنایع شیمیایی و پتروشیمی
- صنایع معدنی و فلزی
- صنایع بازیافت و محیط زیست
- صنایع چوب و کاغذ
- صنایع تولید شیشه و سرامیک
سیستمهای انتقال کابلی و دیسکی چیست و چه کاربردی دارد؟
سیستمهای کابلی و دیسکی از جمله سیستمهای انتقال مواد هستند که در صنایع مختلف برای جابجایی مواد بهکار میروند. این دو سیستم برای کاربردهایی با نیازهای خاص، مانند انتقال مواد حساس یا در فضاهای محدود، طراحی شدهاند. در ادامه بهتفصیل به توضیح این سیستمها میپردازیم.
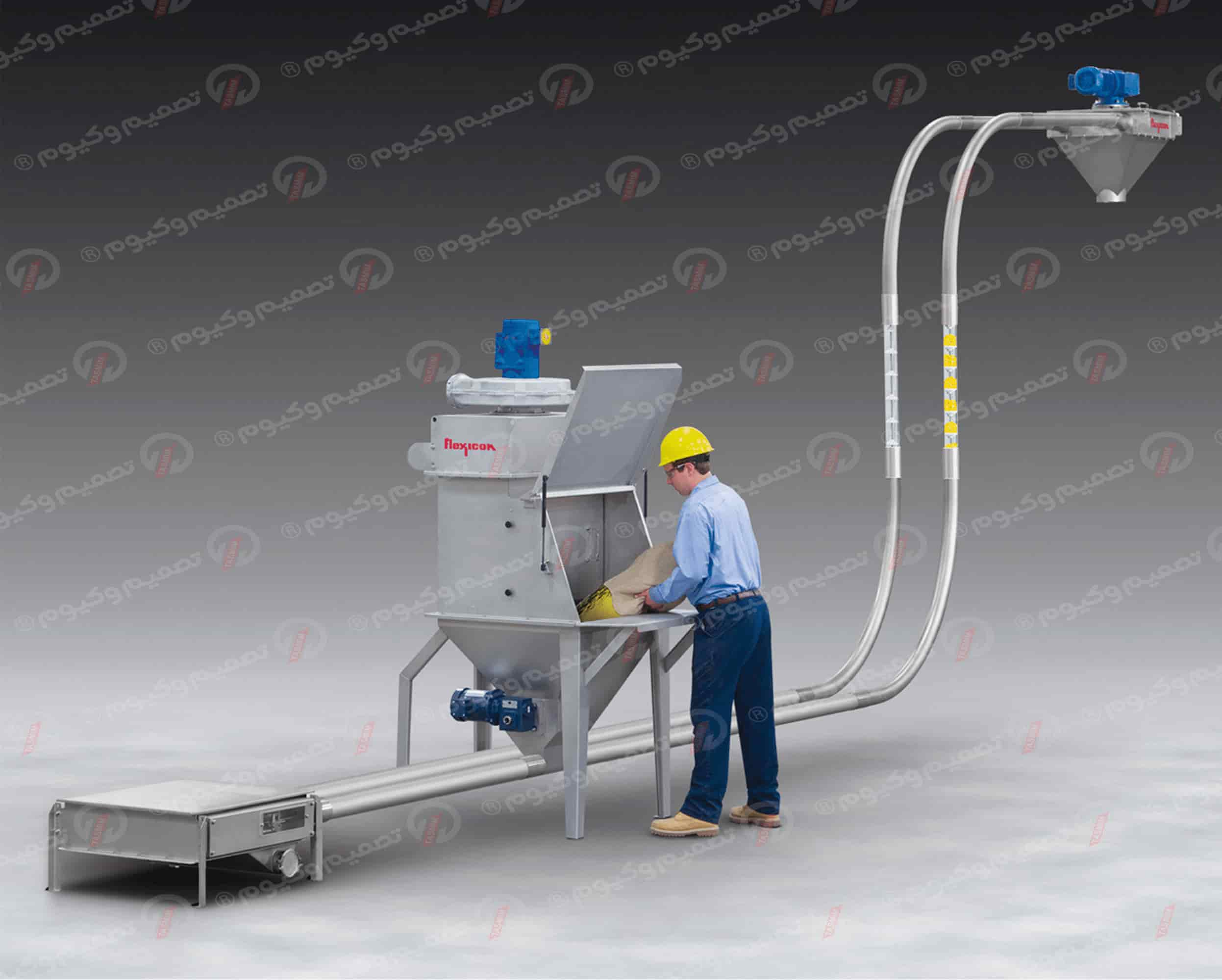
سیستمهای کابلی (Cable Conveyor System)
سیستم کابلی یک نوع سیستم انتقال است که در آن مواد توسط کابلها و چرخدندهها یا سیستم کششی بهصورت افقی، شیبدار یا عمودی جابجا میشوند. این سیستم بهویژه در فضاهای محدود و برای انتقال مواد بستهبندیشده یا در ظروف خاص استفاده میشود.
انواع سیستم کابلی
- سیستم کابلی تکخطی (Single-line Cable Conveyor):
در این نوع سیستم، تنها یک کابل برای کشیدن مواد استفاده میشود. معمولاً برای جابجایی مواد سبک یا بستهبندیشده بهکار میرود.
- سیستم کابلی دوخطی (Dual-line Cable Conveyor):
این نوع از سیستم، برای انتقال مواد با وزن و حجم بیشتر طراحی شده است و دو کابل برای حرکت دادن مواد بهکار میرود.
- سیستم کابلی با واحدهای متحرک (Cable with Moving Units):
در این سیستم، از واحدهای متحرک (مانند گاری یا ظروف خاص) استفاده میشود که به کابل متصل بوده و مواد را جابجا میکنند
اجزای اصلی سیستم کابلی
- کابلها (Cables)
کابلها عموماً از فولاد یا مواد مقاوم به سایش ساخته میشوند و بار اصلی کشش و انتقال مواد را بر عهده دارند.
- چرخدندهها (Pulleys)
برای هدایت و حرکت کابلها از چرخدندهها یا قرقرهها استفاده میشود که میتوانند جهت حرکت سیستم را تغییر دهند
- واحدهای متحرک (Carriers or Conveying Units)
این واحدها مواد را روی کابل نگه میدارند و بهوسیله حرکت کابل، به جلو میروند.
- محرکها و موتور (Motor and Drive System)
برای تأمین نیروی لازم برای حرکت کابلها و واحدهای متحرک از موتورهای الکتریکی استفاده میشود.
- سیستمهای تنظیم (Tensioning Systems)
برای تنظیم کشش کابلها و جلوگیری از گسیختگی آنها در طول مسیر از سیستمهای کششی استفاده میشود.
مزایای سیستم کابلی
- انعطافپذیری در طراحی:
این سیستمها میتوانند در مسیرهای پیچیده و در فضاهای محدود نصب شوند.
- کاربرد در مسیرهای عمودی و شیبدار:
سیستمهای کابلی قابلیت جابجایی مواد در شیبهای مختلف و مسیرهای عمودی را دارند.
- مناسب برای مواد بستهبندیشده یا ظروف:
برای جابجایی مواد داخل جعبهها، بستهها یا ظروف مناسب هستند.
- صدای کم:
سیستمهای کابلی نسبت به برخی سیستمهای دیگر صدای کمتری تولید میکنند.
معایب سیستم کابلی
- ظرفیت محدود:
این سیستمها برای مواد سنگین یا حجم بالا مناسب نیستند.
- هزینه نصب و نگهداری بالا:
نصب سیستمهای کابلی ممکن است هزینهبر باشد و نیاز به نگهداری دقیق داشته باشد.
- محدودیت در انتقال مواد در فواصل طولانی:
این سیستمها بیشتر برای فواصل کوتاه یا متوسط مناسب هستند و برای مسافتهای طولانی کارآیی کمتری دارند.
سیستمهای دیسکی (Disc Conveyor System)
سیستم انتقال دیسکی نوعی سیستم انتقال مواد است که در آن مواد توسط دیسکهای متصل به یک زنجیر یا کابل حرکت میکنند. این دیسکها مواد را در مسیر تعیینشده میکشند و معمولاً برای جابجایی مواد گرانولی، دانهای یا مواد حساس به فشار و آسیب مناسب است.
انواع سیستم های دیسکی
- سیستم انتقال دیسکی با زنجیر (Chain Disc Conveyor)
این سیستم از یک زنجیر برای حرکت دیسکها استفاده میکند و مناسب برای انتقال مواد سنگین و گرانولی است.
- سیستم انتقال دیسکی با کابل (Cable Disc Conveyor)
در این سیستم، از یک کابل برای حرکت دیسکها استفاده میشود و بیشتر برای کاربردهای سبک و مواد حساس به فشار مناسب است.
- سیستم انتقال دیسکی عمودی (Vertical Disc Conveyor)
این سیستم برای انتقال مواد به صورت عمودی طراحی شده است و معمولاً برای جابجایی مواد به ارتفاعات بالا استفاده میشود.
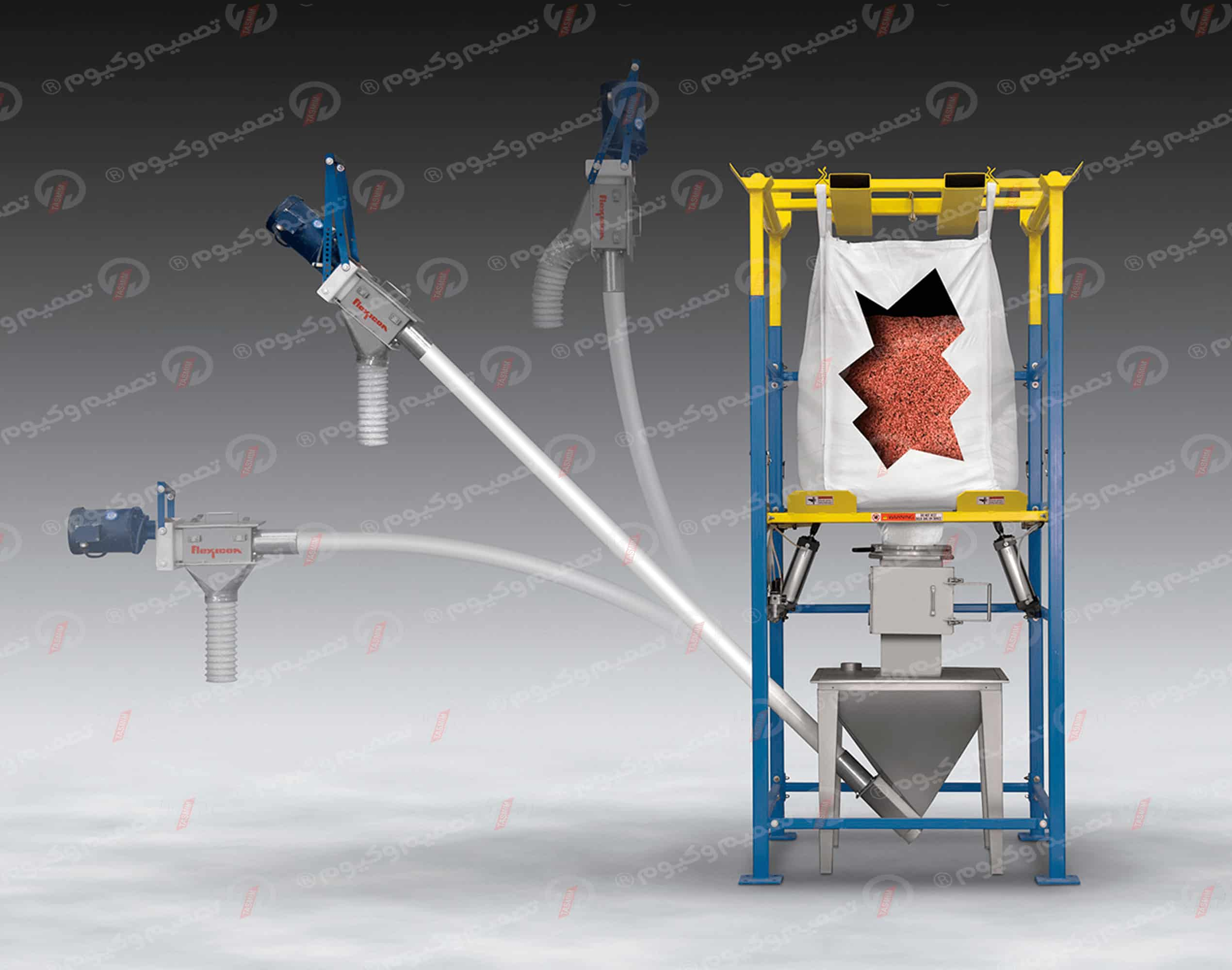
اجزای اصلی سیستم دیسکی
- دیسکها (Discs):
دیسکهای مسطح یا کمی مقعر که مواد را بر روی خود حمل میکنند. این دیسکها بهطور مرتب به یک زنجیر یا کابل متصل میشوند.
- زنجیر یا کابل (Chain or Cable):
زنجیر یا کابلها دیسکها را به یکدیگر متصل کرده و حرکت آنها را در مسیر انتقال انجام میدهند.
- چرخدندهها و قرقرهها (Pulleys and Gears):
برای هدایت زنجیر یا کابل از چرخدندهها و قرقرهها استفاده میشود.
- محرکها و موتور (Motor and Drive System):
نیروی لازم برای حرکت سیستم توسط موتور تأمین میشود.
- سیستمهای نگهدارنده و تنظیم (Support and Tensioning Systems):
برای نگهداری سیستم و تنظیم کشش زنجیر یا کابل از سیستمهای تنظیم استفاده میشود.
مزایای سیستم دیسکی
- مناسب برای مواد شکننده و حساس:
این سیستم برای انتقال مواد حساس به فشار و شکننده، مانند مواد غذایی یا دارویی، مناسب است.
- انعطافپذیری در طراحی مسیر:
سیستم دیسکی میتواند در مسیرهای پیچیده، عمودی یا شیبدار نصب شود.
- انتقال مواد یکنواخت و دقیق:
این سیستم مواد را بهصورت یکنواخت و بدون آسیب دیدن منتقل میکند.
معایب سیستم دیسکی
- ظرفیت محدود:
این سیستمها بیشتر برای انتقال مواد سبک و کمحجم مناسب هستند.
- هزینه بالا:
نصب و نگهداری سیستمهای دیسکی میتواند هزینهبر باشد.
- محدودیت در انتقال مواد در فواصل طولانی:
سیستمهای دیسکی بهطور معمول برای انتقال مواد در مسافتهای طولانی مناسب نیستند.
جمعبندی: انتخاب هوشمندانه برای آیندهای بهرهور
در دنیای رقابتی امروز که بهرهوری، بهینهسازی و کاهش هزینهها در صدر اولویتهای صنایع قرار دارد، انتخاب یک سیستم انتقال مواد دقیق، ایمن و بهصرفه میتواند نقش کلیدی در موفقیت یک کارخانه ایفا کند. در این میان، سیستمهای انتقال پنوماتیک و خلاء بهعنوان پیشرفتهترین راهکارهای مدرن، توانستهاند پاسخگوی نیازهای صنایع حساس، تخصصی و پیشرو باشند.
این سیستمها با قابلیتهایی مانند:
- طراحی کاملاً بهداشتی و بدون گردوغبار
- کاهش قابل توجه استهلاک و هزینههای نگهداری
- امکان اجرای مسیرهای پیچیده و سازگاری با فضاهای محدود
- ایمنی بالا در برابر آتشسوزی و نشت مواد خطرناک
- افزایش راندمان، دقت و سرعت در فرآیند تولید
نقش مؤثری در ارتقاء کیفیت نهایی محصول و بهرهوری کلی خطوط تولید دارند. این مزایا باعث شده تا صنایع بزرگ دارویی، غذایی، شیمیایی، پتروشیمی، آرایشی و حتی الکترونیک، به این فناوریهای انتقال روی آورند و از مزایای آن بهرهمند شوند.
آنچه ما ارائه میدهیم
طراحی و اجرای سیستمهای انتقال پنوماتیک و خلاء
مناسب برای انتقال پودر، گرانول و مواد ریز بدون آلودگی، با طراحی کاملاً بهداشتی، ایمن و قابل اجرا در مسیرهای پیچیده و فضاهای محدود.
سیستمهای مکش صنعتی متنوع و قدرتمند
شامل جاروبرقیهای صنعتی (تکفاز، سهفاز، هواکار، غبارگیر، مرکزی و خاص) و مکندههای صنعتی برای جمعآوری ضایعات، گردوغبار، مایعات، دود و بخارات خطرناک در محیطهای صنعتی.
محصولات تخصصی ما:
- جاروبرقی صنعتی آب و خاک
- جاروبرقی صنعتی
- داست کالکتور
- جاروبرقی صنعتی هواکار
- تله پودر
- جاروبرقی صنعتی خاص
- غبارگیر و مکش دود
- مکنده مرکزی
- مکنده صنعتی سنگین پرتال
- مکنده صنعتی سنگین ثابت
- وکیوم لودر
سوالات متداول
1- آیا سیستم انتقال مواد برای صنایع غذایی مناسب است؟
بله، سیستمهای انتقال مواد پنوماتیک و خلأ برای صنایع غذایی کاملاً مناسب هستند. این سیستمها از لولههای استیل ضدزنگ، طراحی بهداشتی و قابلیت شستوشوی داخلی (CIP) برخوردارند و مانع از آلودگی و تماس مستقیم دست با مواد میشوند. در فرآیندهایی مثل تولید شیرخشک، آرد، قهوه و افزودنیهای غذایی، کاربرد گسترده دارند.
2- آیا نصب این سیستمها در کارخانههای قدیمی امکانپذیر است؟
بله، سیستمهای انتقال مواد بهصورت ماژولار طراحی میشوند و انعطاف بالایی در نصب دارند. بدون نیاز به تغییرات اساسی در زیرساخت کارخانه، میتوان آنها را از طریق سقف، دیوار یا کانالهای موجود اجرا کرد. این موضوع بهویژه برای خطوط تولید قدیمی یا فضاهای محدود بسیار مفید است.
3- تفاوت سیستم انتقال پنوماتیک با کابلی چیست؟
در سیستم پنوماتیک، مواد توسط جریان هوا یا خلأ درون لولههای بسته جابهجا میشوند که برای محیطهای بهداشتی و حساس مناسب است. سیستم کابلی از حرکت فیزیکی کابل یا زنجیر برای کشش مواد استفاده میکند و معمولاً برای مسیرهای خطی و انتقال پیوسته کاربرد دارد. پنوماتیک انعطافپذیرتر و تمیزتر است، در حالیکه کابلی میتواند برای مواد بسیار سنگین در فواصل محدود مفید باشد.
4- آیا امکان انتقال مواد پودری سنگین با این سیستمها وجود دارد؟
بله، سیستمهای انتقال پنوماتیک و با خلأ میتوانند مواد پودری با چگالی بالا مانند سیمان، نشاسته، پلیمر یا پودرهای معدنی را با راندمان بالا و بدون پخش گردوغبار منتقل کنند. طراحی صحیح مسیر، قدرت مکش و سیستم فیلتراسیون نقش مهمی در عملکرد مؤثر آن دارد
5- برای طراحی سیستم انتقال مواد چه اطلاعاتی باید ارائه شود؟
برای طراحی دقیق سیستم، اطلاعاتی مانند نوع ماده (پودری، دانهای، خورنده یا سبک)، چگالی، ظرفیت موردنیاز در ساعت، فاصله و ارتفاع انتقال، شرایط محیطی (دما و رطوبت)، و نیازهای بهداشتی یا ضدانفجاری موردنیاز است. برای دریافت مشاوره تخصصی، میتوانید از طریق صفحه درخواست مشاوره و طراحی سیستم انتقال مواد با ما در ارتباط باشید.